Are you a new welder who needs to get their first plasma cutting tool, or an experienced one who wants to see how far the technology has come in recent years? If the answer to any of these two questions is yes – you’ve come to the right place. Plasma cutters are essential tools for metalwork, no matter whether you’re a hobbyist or make your bread out of it. Buying the right plasma cutter is key to being able to cut metals with precision.
But with so many products nowadays, how do you weed out the bad from the good? Simple – you have to consider the important factors that play a major role in how the tool performs. Without further ado, here’s what you need to pay attention to in order to make the right buying choice.
Duty Cycle
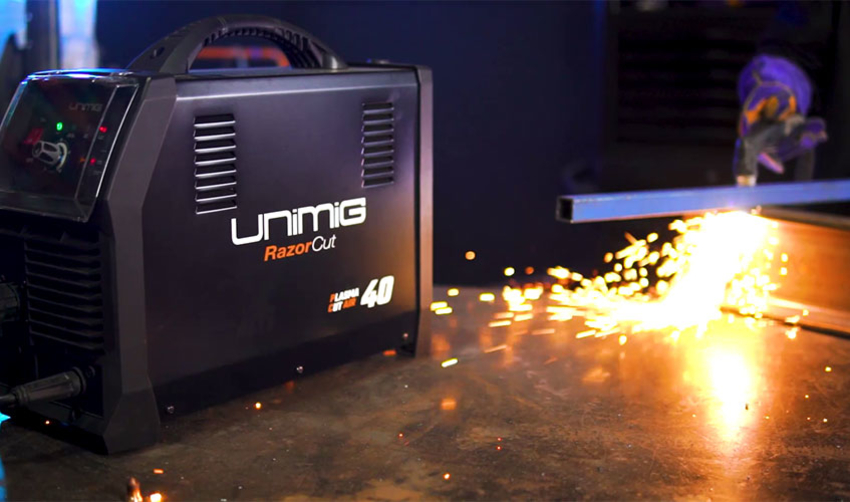
The duty cycle is the most important factor to consider when shopping for most types of power tools. It refers to the longevity of the tool, and it’s mainly determined by the amount of amperage it draws. The duty cycle in tools is typically expressed in percentages, with lower percentages representing shorter periods, whereas larger percentage duty cycles representing more run time. But which duty cycle do you need? Well, only you can answer that question. What do your typical processes look like, how long do they last, and how frequently do you need to use the plasma cutter? In most cases, a 50% duty cycle will be sufficient, especially if you perform manual cutting. However, mechanised cutting requires a significantly higher duty cycle.
Input Power
This factor also plays a role in how well the cutter will perform, as input power will decide how much output power your tool can produce. Additionally, consider the type of electrical outlets in your stores. This is especially important if you’re shopping online, as you may accidentally buy a 110V or 120V cutter, while having 220V or 240V outlets in your garage or store. Since plasma cutters are demanding tools, you’ll want an outlet that’s capable of providing high amounts of power. You may come across dual voltage models capable of handling both 110V and 220V. Furthermore, you have to consider the amperage requirements of your application. For cutting thin metals, you’ll want at least 25 amps; for cutting thicker metals, you’ll want at least 40 amps, and for cutting metals as thick as 2.5cm, you’ll need at least 80 amps.
Cutting Speed
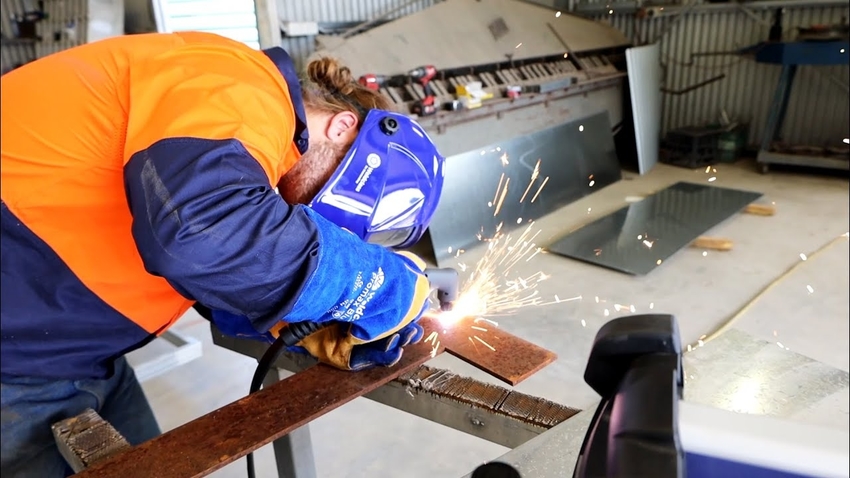
The cutting speed of the plasma cutter also plays a role in the thickness of metals it’s capable of cutting. Cutters are rated for 3 cutting qualities – rated cut, quality cut and severe cut. Rated cut provides the best and highest quality cutting, and is typically used for cutting mild steel or thin steel. Furthermore, it provides max cutting speed, resulting in clean and smooth cuts. The quality cut provides decent quality cutting of thicker metals, but it cuts a little bit longer. Lastly, severe cutting is capable of cutting the thickest of metals, but it’s also the slowest. On the downside, the cutting quality will be rather poor, so you’ll need to perform some post-cut cleanup.
Inverter
Some cutters feature a built-in inverter, while others don’t. You can usually tell if the one you’re looking at has one by its price tag. If you frequently work outdoors or in remote areas, having an inverter can come a long way. Basically, the inverter will take DC power and feed it through a high-frequency transistor. This can add a whole new world of portability and functionality to the tool. Furthermore, cutters with inverters are more efficient in using the power fed to them.
Portability
The ideal level of portability for you will come down to personal preference. If you’re only going to use the cutter in your garage or workplace, you don’t need a portable cutter. However, if you’re going to travel with the cutter and work in multiple locations, then portability is paramount. Two basic factors play a major role in how portable the cutter is – size and weight. Things like having a built-in inverter and air compressor also make it more compact. Furthermore, things like handles, shoulder straps and long cables can also make the job easier. Last but not least, some plasma cutters come with built-in storage where you can store consumables.
Replacement Parts and Consumables
You want the cutter you buy to have widely available replacement parts and consumables. This is usually guaranteed when buying a plasma cutter from a well-known brand, as opposed to buying from a no-name brand. Buying from a known brand usually guarantees quality, and most cutters will come with a lengthy warranty, giving you peace of mind that your investment is backed. Some consumables you’ll have to stock up on are electrodes, shield, nozzle, swirl ring, etc. The nozzle and electrode, especially, will have to be replaced quite frequently.